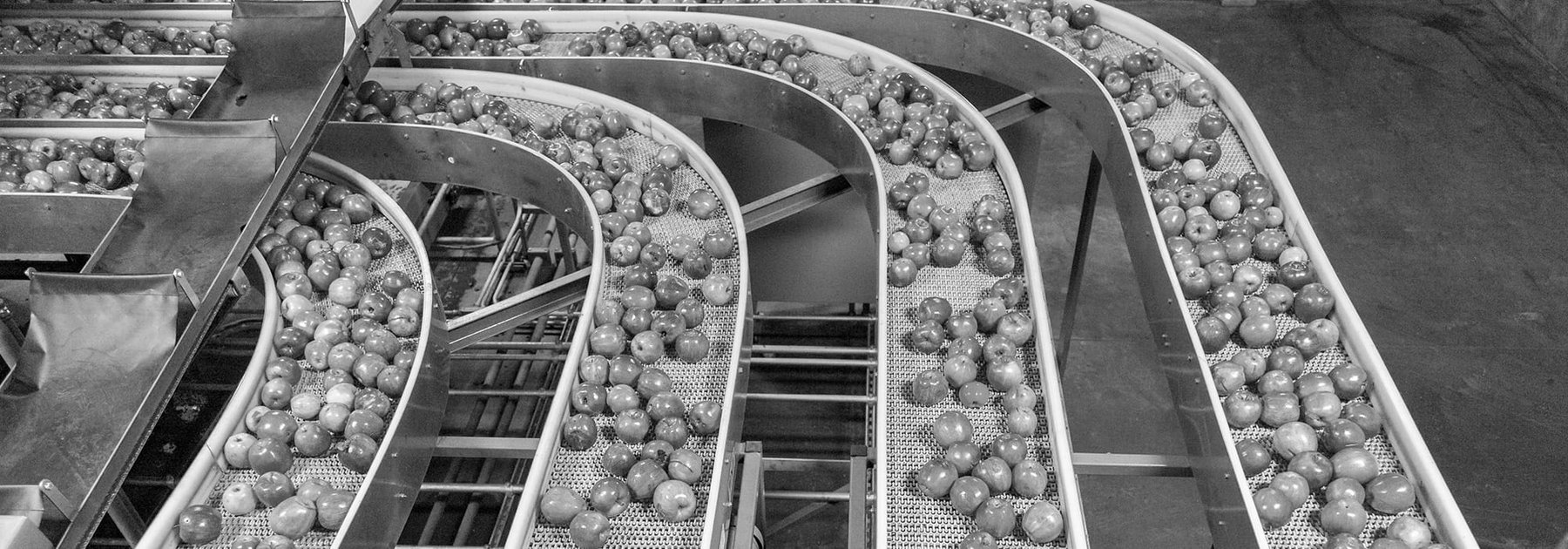
High-speed optical sorting
We partner with leading experts in optical sorting technology for meat and diary products.
A wide range of optical inspection quality control solutions are available, for products ranging from bacon ends and pieces, through to cheese and meat slices. The specialist inspection equipment also has benefits for other sectors like salads in produce.
Increased production speeds
Reduce waste
Labour saving
Quality and consumer safety
Foreign Material Inspection System
The Low-Density Foreign Material System developed by ProSpection sets the standard in the industry for solving low-density foreign material issues. These systems efficiently scan both the upper and lower surfaces of products, handling rates ranging from 10,000 to 40,000 pounds per hour. The FMI Systems possess the capability to identify low-density materials as small as 2mm square. With IP69-rated equipment, they are designed for wash-down compatibility and can seamlessly integrate into operations with 10-foot sections.
Find out more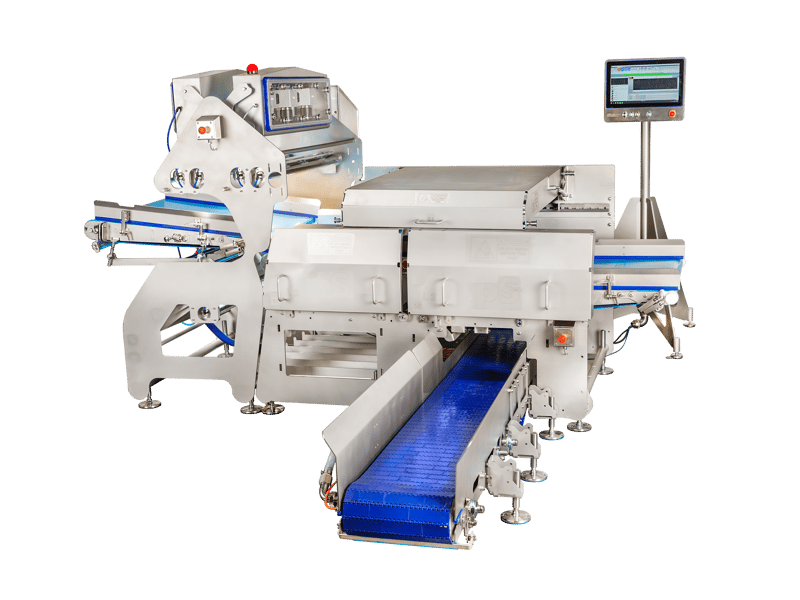
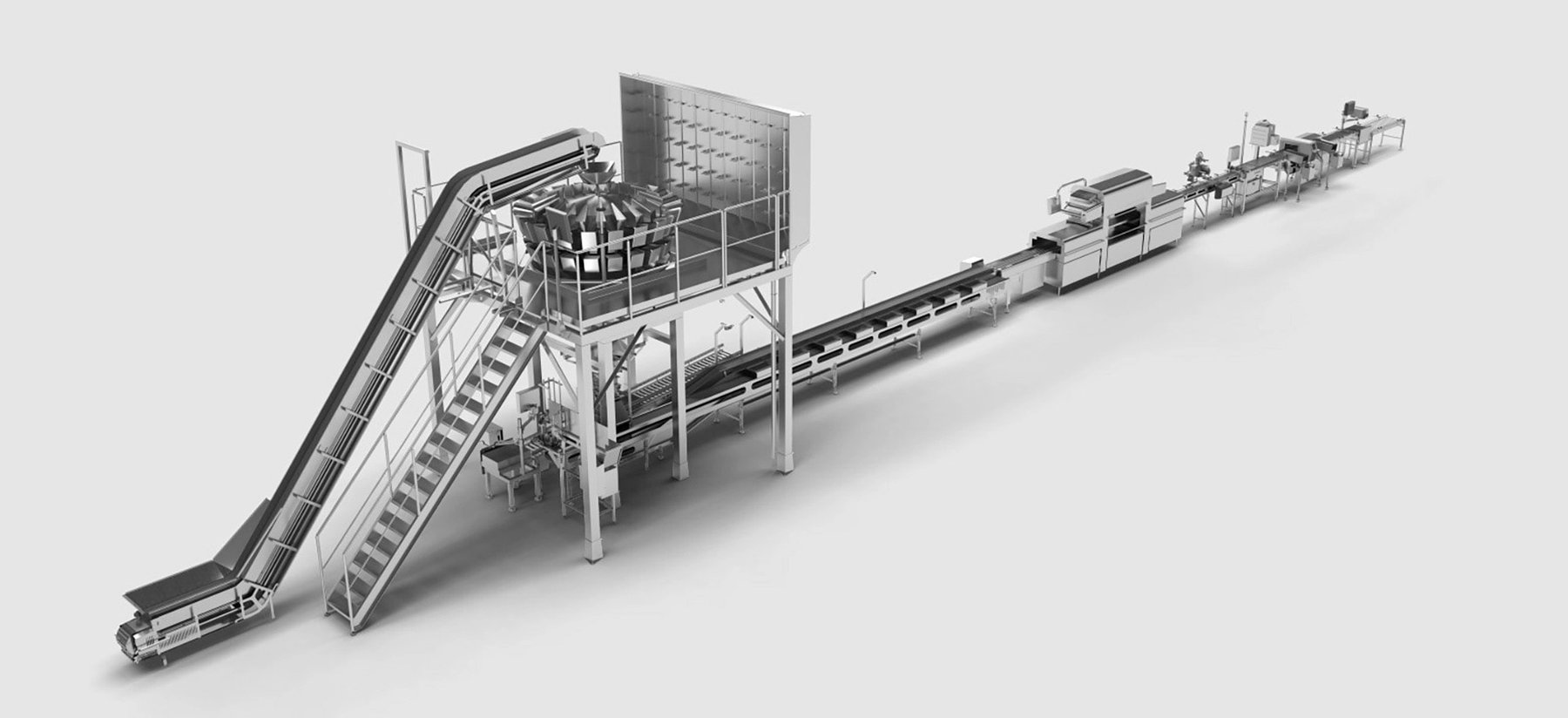
How can you benefit from our expertise?
Whatever your production line requirements, we have the expertise that can really make a difference to your overall efficiency and operating costs. Get in touch with us today to arrange a consultation with our expert team and let’s explore the possibilities.
Full line solutions
We design and project manage the installation of bespoke machines across the full production line. Our network of partnerships has helped us to expand our range to offer automated full line solutions which are flexible enough to fit around your business needs and respond to a changing market.
-
Case Study
From Manual to Precision – Automating Rice Depositing with Sealpac UK & Partners
The Challenge Our Product Manager - Gary Tufnell and Sales Manager - Tom Hughes approached a leading food manufacturer, who had a persistent problem:...
Read the full Case Study -
Case Study
Assisting with Labour shortage by automating monotonous processes
The Challenge With a demanding production schedule and limited access to reliable short-term labour, this customer faced two major hurdles: keeping up...
Read the full Case Study -
Case Study
Successfully Relocating Packaging Solutions To A New Site For A Poultry Processing Company
Relocating Packaging Solutions In A Poultry Processing Company The Challenge The challenge presented to us involved relocating three A series...
Read the full Case Study -
Case Study
Food safety – Inspection and detection
Automated food quality and safety inspection solutions The Challenge The presence of micro-holes in food packaging is a particularly critical problem in...
Read the full Case Study