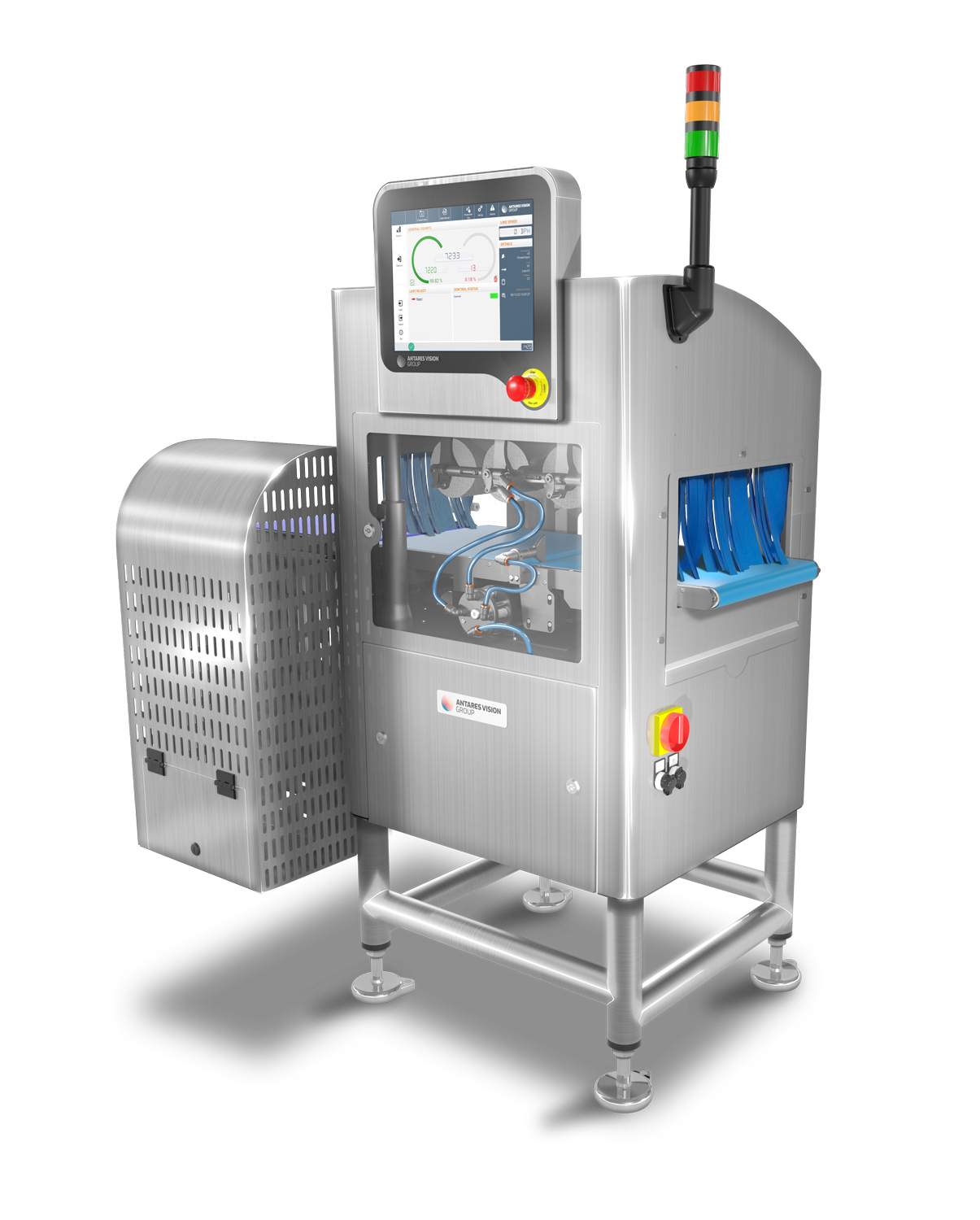
Leak and Seal Inspection
Antares Vision Group offers advanced in-line solutions for seal inspection and leak detection, ensuring 100% of production is thoroughly checked for food safety and quality.
Using cutting-edge IR spectroscopy technology, the leak detection system identifies CO2 leaks caused by holes or micro-holes in packaging or seals, all without affecting line speed or the modified atmosphere inside the package. The seal inspection system detects organic material, such as food residues or external agents, in the seal area. For rigid containers, the Vacuum/Pressure Control system verifies the integrity of cans and twist-off caps using pressure variation analysis, while the PCS Liquid Food system monitors pressure conditions in trays and jars to detect leaks or packaging deformation.
Real-time data updates and automatic rejection of defective packages prevent compromised products from reaching the shelves, maintaining the highest quality standards. We can build our machines fully to retail specification.
In-Line Leak Detection LDS IoT CO2
The LDS 700 helps reduce costs associated with waste by optimising the sealing process, minimising withdrawals or recalls, and eliminating labour hours lost to manual inspections. With our advanced inspection systems, you can trust that your products will reach your customers safely and in top quality. Using IR spectroscopy technology, the system detects CO2 leaks caused by holes or micro-holes in packaging or seals, all while maintaining line speed and preserving the modified atmosphere.
Benefits:
-
Leak detection and seal check (holes and micro-holes)
-
In-line and Non-destructive controls
-
Checks on 100% of production
-
Laser spectroscopy
-
Reduction of costs due to product returns
-
Reduction of costs due to personnel involved in spot checks
-
Reduction of costs due to destructive checks
-
Sustainability Improvement: less quantity of plastic produced and less food waste
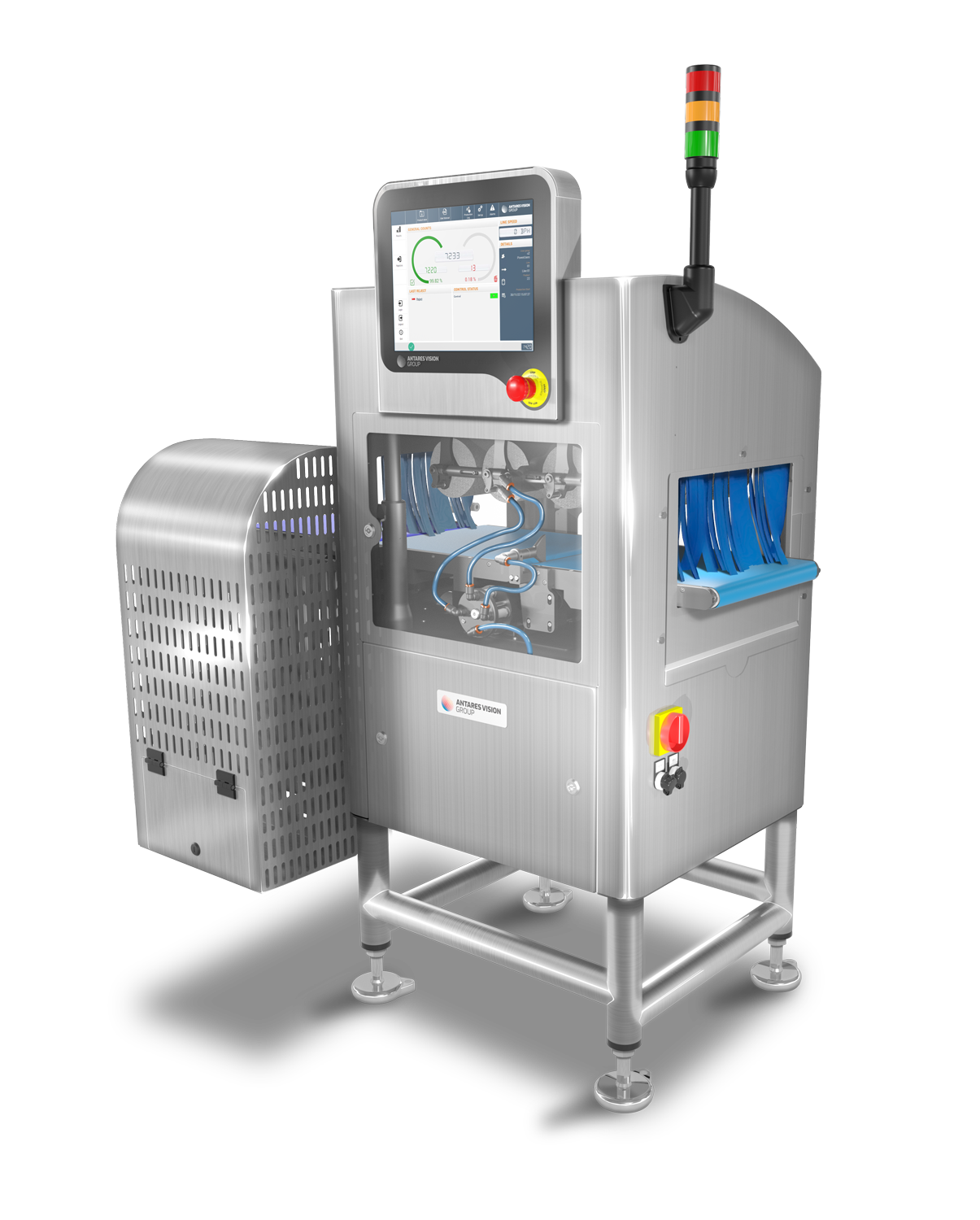
Seal Inspection – SIS 700
The SIS 700 helps lower costs associated with product recalls and labour hours wasted on manual inspections. With our inspection systems, you can trust that your products will be safe and high-quality when they reach your customers. Using advanced hyperspectral technology, the system’s camera selects the optimal wavelength to ignore packaging material and focus solely on organic material in the seal area. This ensures effective inspection, regardless of whether the foil is transparent, coloured, or opaque.
This solution can be custom-designed to mount directly onto a thermoformer. For more details, please contact us to discuss your specific requirements.
Models:
- SIS 700 VA (for transparent foil)
- SIS 700 IR (for coloured or opaque foil)
Benefits:
- Regardless analysis of the colour and the graphics on the film
- In-line and non-destructive inspection
- Checks on 100% of production
- Hyperspectral Technology
- Reduction of costs due to lack of returns
- Reduction of costs due to personnel involved in spot checks
- Reduction of costs due to destructive checks
- Sustainability improvement: less quantity of plastic produced and less food waste
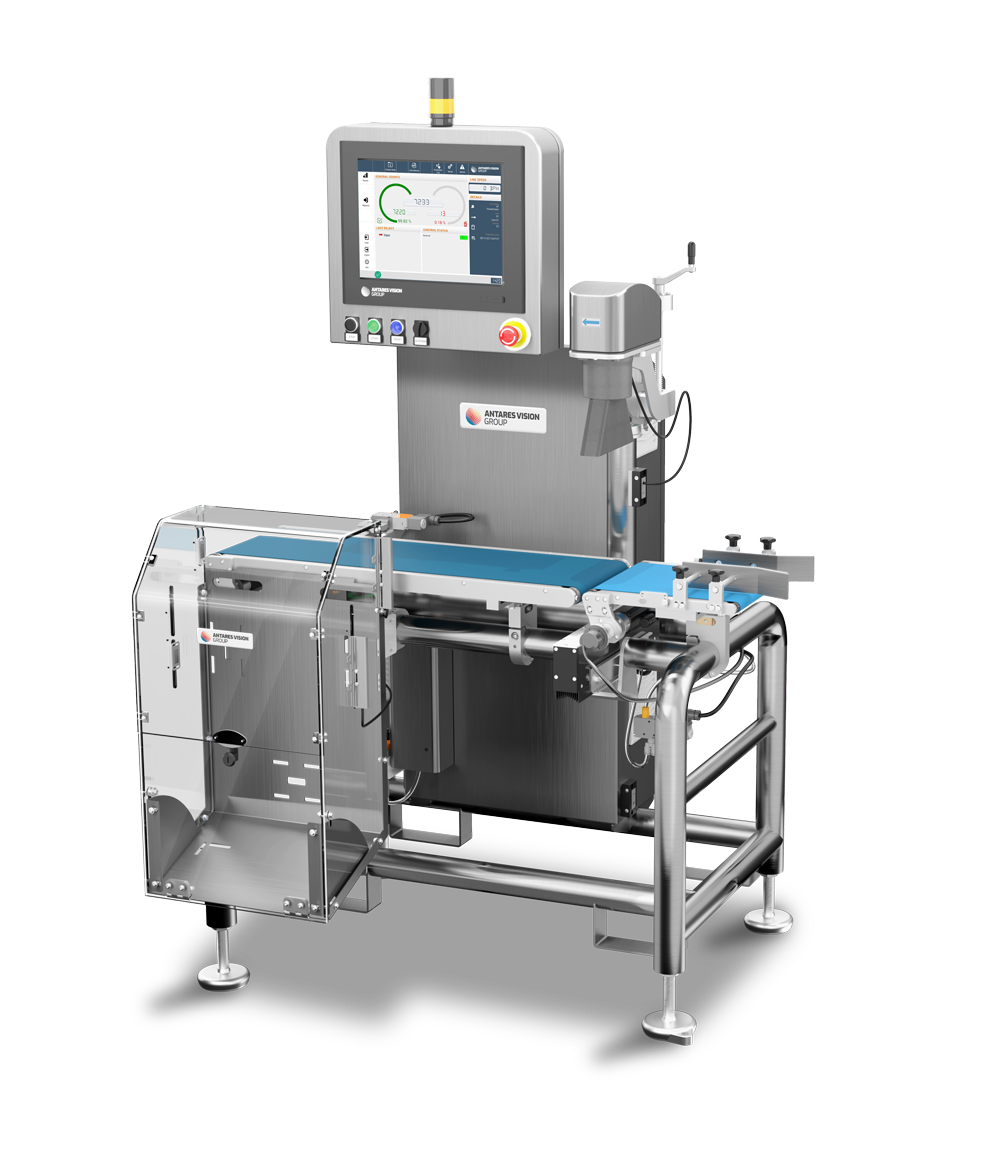
PCS Liquid Food - Bottle Leak Detection
PCS Liquid Food is a high-performance in-line leak detection system designed for food preserves and baby food. Using laser spectroscopy, it precisely measures the pressure in the headspace of each individual sealed container, regardless of cap type or material. Installed after the capping phase, it verifies vacuum formation in hot-filled products or correct nitrogen dosing in PET bottles. PCS ensures accurate, real-time monitoring, promptly identifying leaks, capper or doser malfunctions, and pressure inconsistencies. This enables early intervention, reduces waste, improves long-term sealing, and ensures only perfectly sealed products continue along the production line—protecting both product integrity and shelf life
Benefits:
- Laser Spectroscopy Technology
- Direct measurement of pressure in the headspace of the bottle
- Rapid, reliable and non-destructive analytical measurement
- Non-contact inspection, no components subject to wear
- Small footprint, hygienic design, washable structure
- User-friendly interface
- New format set up in just 5 minutes
- Statistics and production history
- Alarm and event history
- I/O diagnostics, parameters, and signals
- Oscilloscope
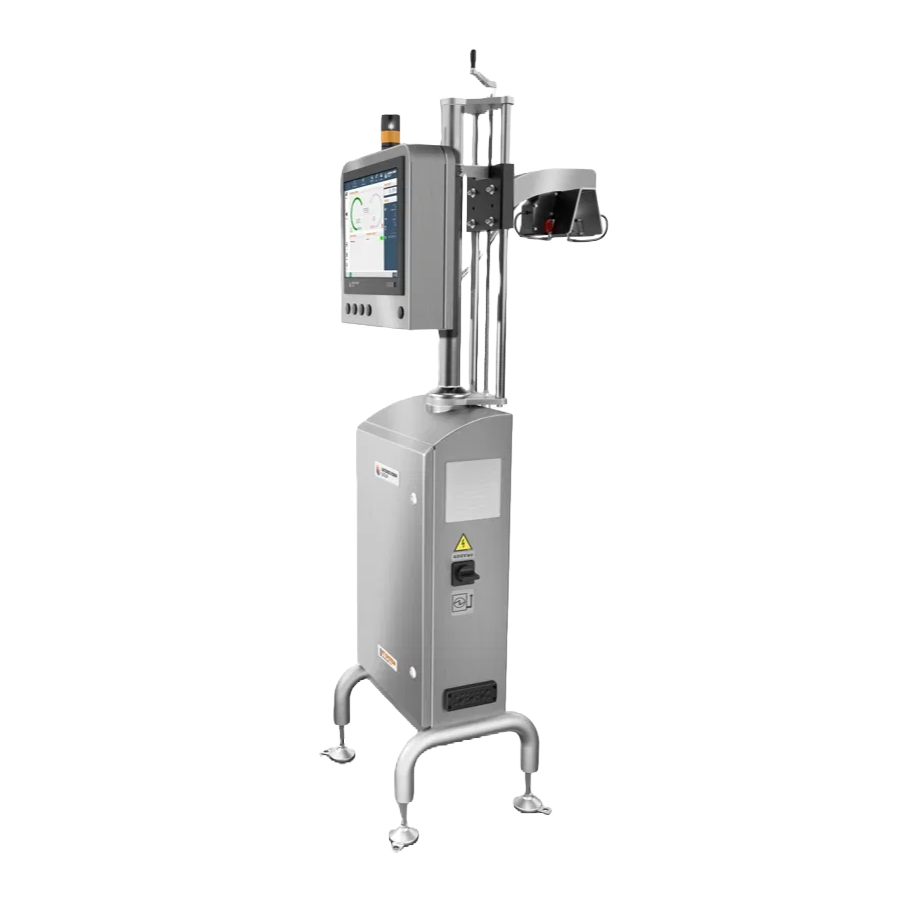
Vacuum/Pressure Control for Cans and Twist-off Caps
Vacuum/Pressure Control for Cans and Twist-off Caps is an in-line inspection system that checks the internal pressure or vacuum of sealed containers, such as pressurised cans and twist-off cap jars. Using advanced PX sensor technology, it detects faults in fillers, seamers, cappers, closures, and the product itself—such as fermentation or CO₂ dosing issues. It ensures product safety, quality, and shelf-life by automatically rejecting containers with over or under pressure, while providing detailed production data and supporting consistent process control.
Benefits:
- Inductive technology
- Maximum accuracy
- Minimum maintenance
- Independent structure for eliminating noise and vibration
- No change in the existing line for installation
- Production records
- Expandable with other inspections
- User-friendly interface
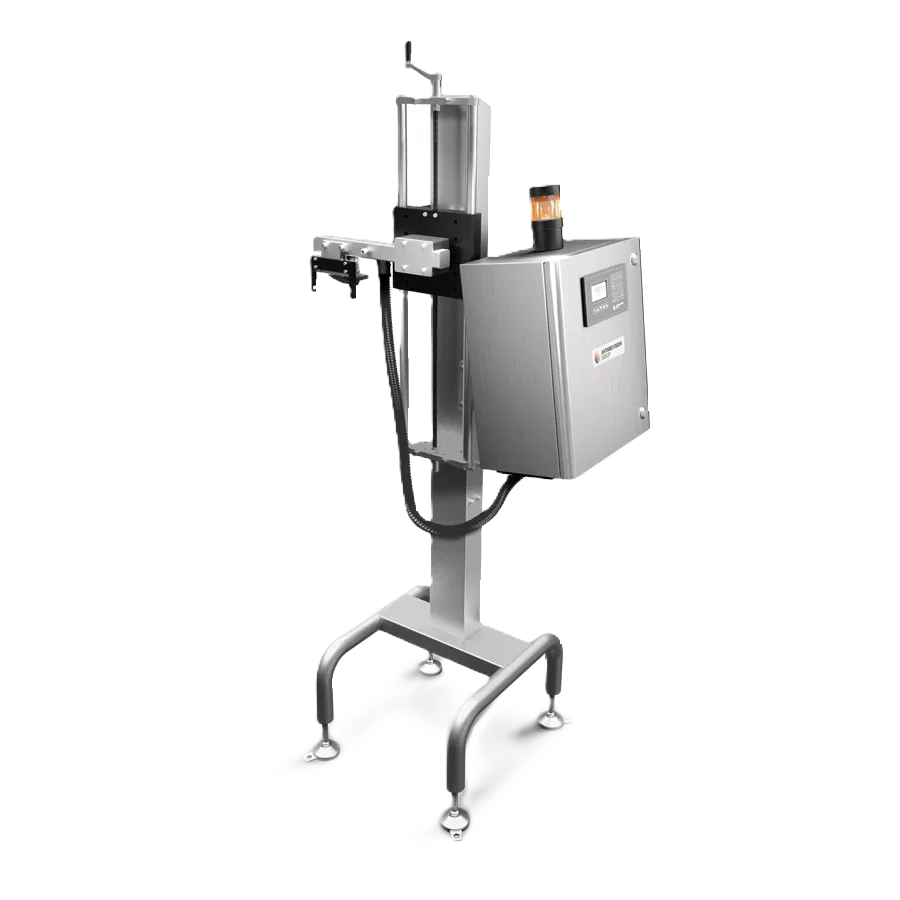
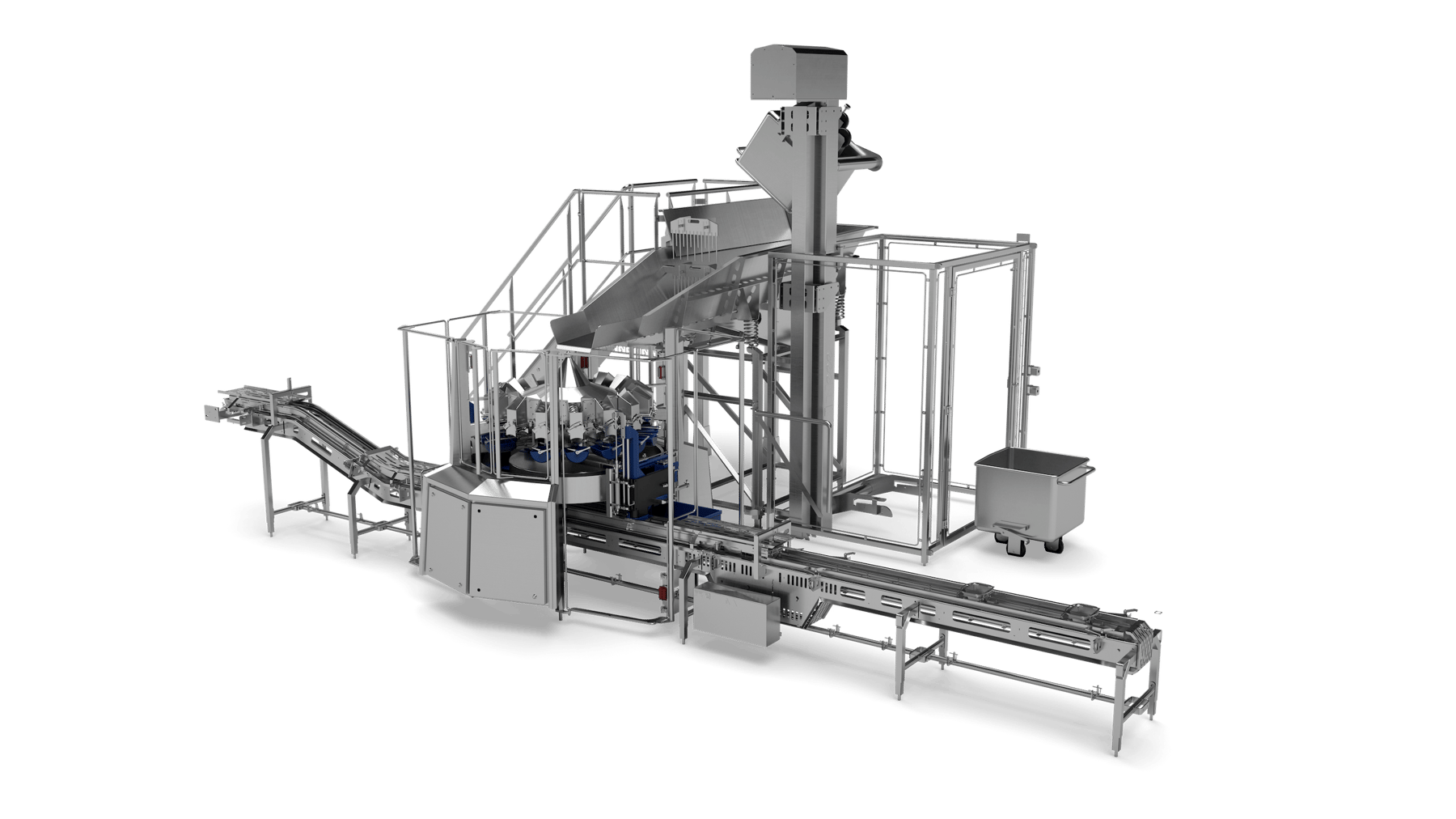
How can you benefit from our expertise?
Whatever your production line requirements, we have the expertise that can really make a difference to your overall efficiency and operating costs. Get in touch with us today to arrange a consultation with our expert team and let’s explore the possibilities.
Full line solutions
We design and project manage the installation of bespoke machines across the full production line. Our network of partnerships has helped us to expand our range to offer automated full line solutions which are flexible enough to fit around your business needs and respond to a changing market.