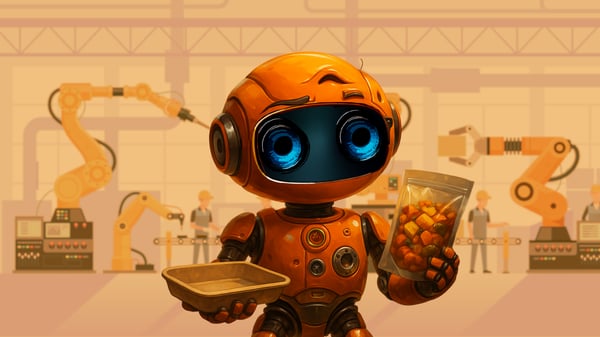
How to Choose Your Right Packaging Format?
In today’s competitive food industry, choosing the right packaging format is crucial—not only for product protection, but also for brand appeal, ...
Continue reading?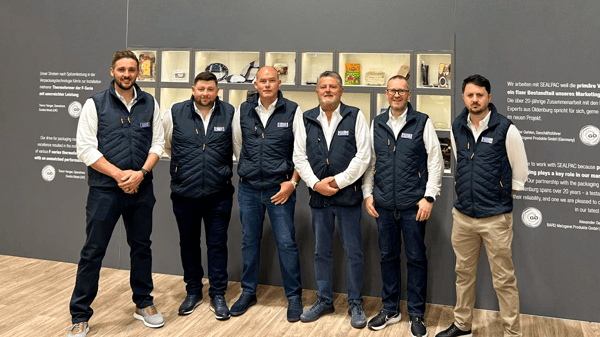
IFFA 2025 – A Show to Remember for Sealpac UK & Partners
What a buzz IFFA 2025 turned out to be! From start to finish, it was one of the most exciting and successful exhibitions we've ever attended – and that’s...
Continue reading?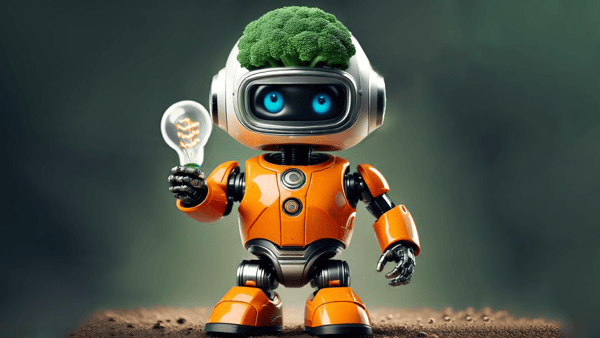
Veganuary with Sealpac UK and Partners
As Veganuary continues to inspire consumers to explore plant-based lifestyles, businesses are globally adapting to meet the growing demand for vegan...
Continue reading?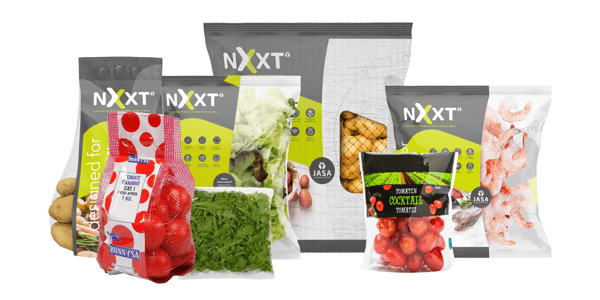
Why Bagmaking Matters in Modern Packaging
In today’s dynamic world of food production and consumer goods, packaging has evolved beyond its primary function of containment. It now serves as a...
Continue reading?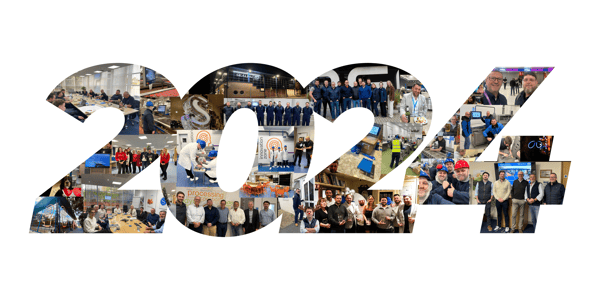
Wrapping up a Record Breaking Year - 2024!!
As we close the chapter on 2024, it’s clear this year has seen one of Sealpac UK's remarkable growth, milestone innovation, and collaboration. From...
Continue reading?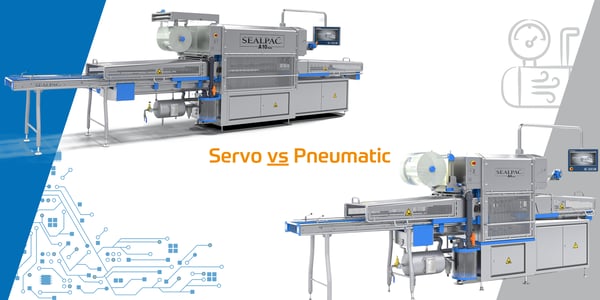
Evolution of Machine in Production Industry: From Pneumatic to Servo
In today’s rapidly advancing food processing and packaging industry, the shift from pneumatic to servo-driven machines has revolutionised efficiency,...
Continue reading?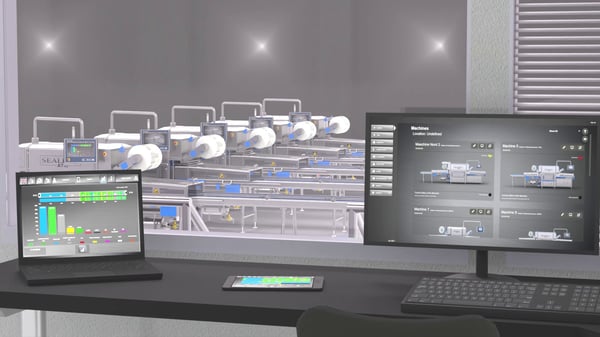
Sealpac UK's Approach to Industry 4.0: Integration with OPC UA
With the fast evolving food processing industry, adopting these fast-paced digital technology has become a necessity. Industry 4.0 brings smart automation...
Continue reading?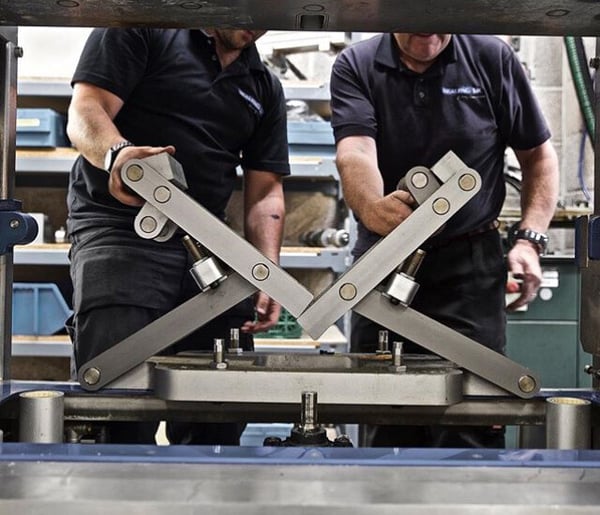
Planned Preventive Maintenance (PPM) - Sealpac UK's POV
In the food processing industry, maintaining high levels of efficiency, safety, and quality is critical. One of the key strategies to achieve this is...
Continue reading?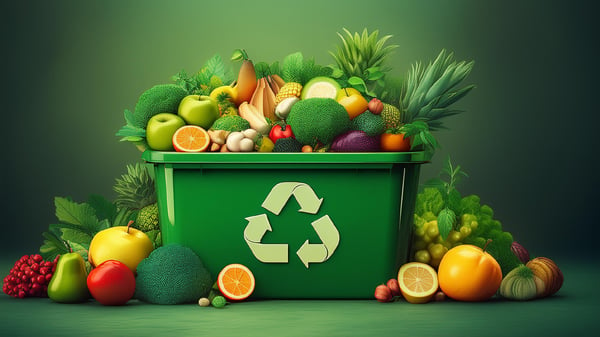
Reducing Food Waste: A Sustainable Partnership with Sealpac UK
In an era where sustainability is more than a buzzword, reducing food waste has become a global initiative. At Sealpac UK, we have always been at the...
Continue reading?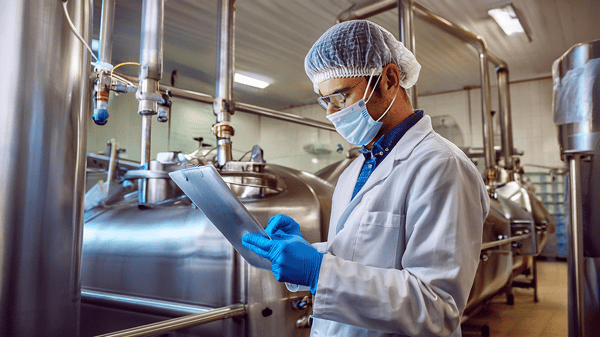
The Importance of Hygienic Processing in the Food Production Industry
In the food production and packaging industry, maintaining strict hygiene standards is essential for ensuring food safety, preventing contamination, and...
Continue reading?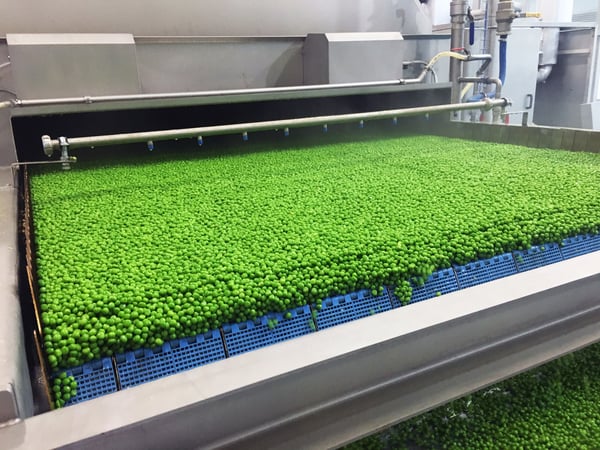
The Role of Blanchers in Ensuring Food Quality
When it comes to food processing, where efficiency and quality are absolutely key, industrial blanchers are vital equipment for preserving and preparing...
Continue reading?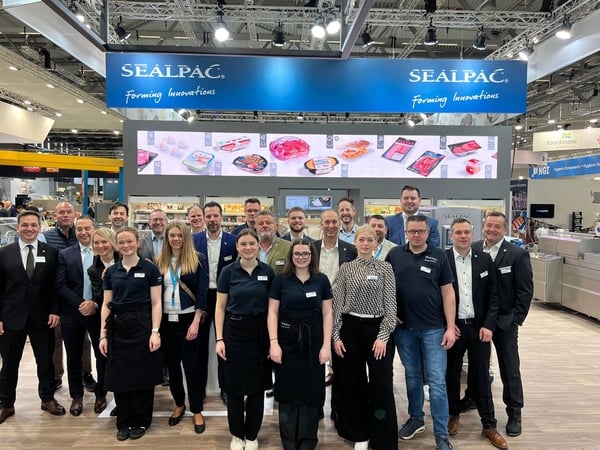
Anuga Food Tec 2024
Last week, our team headed up to Cologne for the highly anticipated Anuga Food Tec 2024. And if you have been keeping up with our LinkedIn posts, you...
Continue reading?